Acrylic Roof Coatings: Acrylic roof coatings have the longest history within the industry. They were first formulated for roofing during the mid-1970s . Acrylic roof coatings are water-based composites that are very UV stable with high durability and elongation built into the resin structure. Acrylics are the most user-friendly of all roof coatings thanks to the water clean-up and low reactivity. They also tend to be the safest related to exposure.
Strengths:
- High performance in any climate zone.
- Most cost-effective roof coating solution.
- Great in positive slope applications.
- Long term maintenance of a High Solar Reflective index.
- Highly versatile in hybrid situations.
Weaknesses:
- Acrylics can lose mils as they age. (Approximately .5 mils per annum.)
- Cold temperatures are of concern with Acrylics due to their water-based chemistry. They must be installed at temperatures 40 °F or higher.
- In higher humidity climates, dew is a concern. Acrylic coatings cannot be applied if dew is imminent or if the saturation point and temperature are within 5 degrees in order to avoid a wash-off.
- Acrylics swell under ponding water requires them to be used with caution in areas of known ponding water.
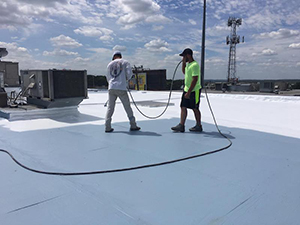
Polyurethane Roof Coatings: Polyurethane roof coating systems are higher performing systems than typical water-based systems. Polyurethanes represent two main chemistries. Aliphatic and Aromatic.
Aromatic chemistries tend to be used as basecoats in most coating systems because as they are less UV stable than Aliphatic chemistries. Typically, these Aromatic Urethanes have higher endurance, but lower elongation compared to an Aliphatic . Most manufacturers utilize Aliphatic Urethanes as Topcoats in their system because they need superb UV stability, better water swelling resistance, and a really high combination of lastingness and elongation.
Strengths:
- High endurance paired with high elongation.
- Good water swelling resistance.
- Particularly good traffic & impact resistance.
- Can be applied in colder, more variable climatic conditions.
- Typically, they’re solvent based or 100% solid chemistries.
Weaknesses:
- Urethane Coating formulas contain many known carcinogens like aliphatic hydrocarbon solvents, Isocyanate , and others.
- Many Urethanes have a robust odor which has to be addressed with building inhabitants.
- Urethanes are very reactive and sensitive to external factors. If applied too thick or within the wrong climatic conditions, they’ll “pinhole,” causing little holes to occur within the film of the coating.
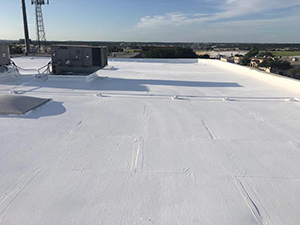
Urethanes may also trap air as they cure and “off gas.” In some cases, they will cure too fast which can trap air and cause bubbling within the film. These weaken the strength and can compromise the integrity of the coating system.
Silicone Roof Coatings: Silicones are moisture-cure chemistries that may be both solvent-based, as well as High Solids (HS) 100% solids. In the case of the 100% solids Silicones, the resin is used as the flow agent. There are two categories of Silicone coating formulas: Alkoxy cure mechanism and Oxime cure mechanism. Though more important for the manufacturing process, there are some slight differences which may be noticed by the applicator. In general: Alkoxy cure silicone products aren’t required to be mixed on-site before application, and they tend to cure faster than Oxime cure mechanisms.
Strengths:
- Silicones contain strong OH bonds within their resin structure. This stability makes them very resistant to UV degradation.
- Due to their inorganic nature, Silicones are highly resistant to fungal or mold growth.
- Silicones don’t get hard and brittle.
- Strong resistance to ponding water, making them ideal for low slope roofs.
- Adhesion to a myriad of substrates which reduces primer use.
- HS Silicones ‘ wet mil thickness is up to dry mils. You lose no product to evaporation or shrinkage.
- Low & Zero percent solvent formula options meet or exceed all VOC regulations in US and Canada.
Weaknesses:
- Reduced tensile strength and Elongation compared to other roof coatings.
- Poor tear strength. Not recommended on metal roofs.
- Silicone roof coating surfaces attract more dirt than other coatings. This causes a major reduction in reflectivity over time when put next to other roof coating chemistries.
- Silicone only sticks to silicone. Once Silicone is installed, you must use Silicone based products to repair and recoat it.
- Silicone products require high pressures and volume outputs to spray and they’re tougher to figure with than other chemistries.
SEBS & SBS Roof Coatings: SEBS (Styrene-Ethylene-Butadiene-Styrene) and SBS (Styrene-butadiene-styrene) roof coatings fall under the category of “Rubber” Coatings. These coatings are manufactured by utilizing a block rubber polymer that’s then dissolved in a hydrocarbon solvent. Performance additives are added to complete the formulation. These varieties of coatings cure by solvent evaporation. Rubber coatings offer significant advantages including nearly 0% moisture swell rate, extremely low vapor permeance, and strong strength and elongation features.
Strengths:
- Most rubber coatings perform well under ponding water issues as they have a low moisture swell rate. In some cases, it’s as low as 0%.
- Extremely low vapor permeance rate.
- Strong durability.
- High % Elongation.
- Exceptionally good launderability. (Stays whiter longer than many coating chemistries)
- Strong Chemical resistance.
Weaknesses:
- High Solvent formulas typically don’t meet local VOC requirements.
- Two coat system.
- Spray Machine used must be stronger than typical Acrylic Coatings.
- Solvent cleanup instead of water which suggests more safety protocols.
- Applicators need protection from exposure to some raw materials within the formula.